In the course of friction between textiles and other objects, the color loss or the degree of contamination of the rubbed object is affected by many factors. There are two ways to cut off the color: one is the dye on the textile off or fade, contaminated in the friction surface; the other is the dyeing fiber off, adhere to the surface of the friction object. In practice, the dye off is the main reason for staining.
Although there are some differences in the covalent bond strength and adhesion between the reactive dyes of different chemical structures and cellulose fibers, the effect of wet fastness on dyeing of dyed fabrics is basically the same. When the dyed fabric is wet rubbed, the covalent bond between the dye and the fiber does not break and produces a float. Dye transfer occurs usually does not form a covalent bond with the fiber, but only van der Waals force to produce adsorption, that is, floating color. One of the main causes of floating color is the excessive amount of dye. When the moisture is rubbed, the amount of color is almost linearly related to the depth of dyeing. When dyeing is dark, the dye concentration used is high, but it should not exceed the saturation value. Because the excess dye can not be combined with the fiber, only in the fabric surface accumulation and the formation of floating color, seriously affect the fabric wet rubbing fastness.
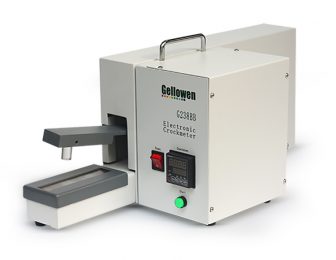
The directness and diffusivity of the dye are also closely related to the rubbing fastness. Directly high reactive dyes, although the dye uptake rate and fixation rate is high, but the diffusibility is poor, more difficult to diffuse into the fiber inside, causing the surface floating color, the hydrolysis of the dye is not easy to wash, easy to contaminate the friction object. Diffusible dye easily into the fiber inside, is conducive to improving the friction fastness, while their washing is also better, easy to spread out from the fiber inside. For some poorly stable dyes, especially dyestuffs, even if the unfixed dye on the surface of the fabric is washed and placed for a certain period of time, the hydrolyzed dye will diffuse from the interior of the fiber, resulting in poor soaping and rubbing fastness.
Different microstructure and morphology of different fibers, dye diffusion rate and the degree of penetration is also different, so the dye in different fibers on the fixation rate and distribution are also different. High fixation rate, less hydrolytic dye, easy to wash, fast rubbing fastness; fiber surface smooth, organizational structure and friction coefficient is low, the same can also improve the rubbing fastness. Common several kinds of fabric structure of the fabric, the friction factor size order: plain weave fabric> twill fabric> satin fabric. Some thin fabrics (synthetic fibers or silk fabrics), due to the relatively loose fabric structure, dry friction, the sample under the action of pressure and friction will follow the movement of the friction head part of the slip, so that the friction resistance But the friction efficiency is improved, but in the case of wet friction, the moisture absorption is extremely low, the water swelling effect is not obvious, and the presence of water acts as a lubricant, causing it to wet Friction fastness is better than dry friction fastness.As for some surface rough sugar or matte, woolen fabric, in dry conditions, the surface rough, hard, frictional resistance, dry color fastness to decline.
The pretreatment of the fabric has a great effect on the rubbing fastness. Unprocessed cotton fibers in the wet conditions will be swollen, increased friction, fiber strength decreased, which are colored fibers break, shedding and color transfer to create the conditions. Therefore, the appropriate pre-treatment of cellulose fibers before dyeing, such as mercerizing, singeing, cellulase cleansing treatment, can improve the fabric surface finish and hair effect, reduce frictional resistance, reduce the floating color, thereby effectively improving the fabric Of the moisture fastness to rubbing.